Dry Process Fibreboards (MDF)
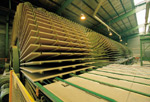
Description
Dry process fibreboards are engineered wood-based sheet materials made by bonding together wood fibres with a synthetic resin adhesive. The term ‘dry process fibreboards’ is a generic term so called by virtue of the manufacturing process.
Within this description, the most common class of board is Medium Density Fibreboard (MDF) although this in itself is a generic class, which can be for marketing purposes sub-divided into panel types differentiated principally by their density, i.e.
High Density MDF (HDF)
Low Density MDF (LDF)
Ultra Low Density MDF (ULDF)
Since 1966 when the first MDF was produced commercially in Deposit, New York State, USA, the market for MDF has increased dramatically world-wide. The first MDF was produced in Europe in 1973 and today European production rivals that in the USA.
Because of its availability in a wide range of thicknesses and the ability to be machined and finished to a high standard, dry process fibreboards have been accepted in a wide range of applications both in construction and also furniture, where in both cases it has substituted solid timber and also other wood-based panels in particular applications.
The development of value added variants with enhanced mechanical performance and improved performance in the presence of moisture and fire have further aided the applications available.
MDF can be manufactured with either softwood or hardwood species. The majority of MDF manufactured is composed mainly of softwood although some individual brands may contain a higher percentage of temperate hardwood depending on the location of the factory to the local forest resource.
The constituents of a typical standard MDF manufactured in the United Kingdom or Ireland are 82 virgin wood fibre (wholly or mainly softwood), 10% synthetic resin binder, 7% water, less than 1% paraffin wax solids and less than 0.05% silicon. The most common binder is urea-formaldehyde although depending on the grade and end use of the product other binders may be used, i.e. melamine urea-formaldehyde, phenolic resins and polymeric methylene di-isocyonate (PMDI).
A typical process involves reducing wood down to small chips, which are then thermally softened and mechanically refined into fibres, which are then mixed with a synthetic resin binder. The resinated fibres are dried and then formed into a mattress ready for pressing.
The mattress is pressed between heated polished press plates to the desired thickness. For thick boards more than one mattress may be ‘piggy backed’ together.
Appearance
MDF has smooth sanded surfaces, it has a homogeneous construction and is typically pale straw in colour. For identification purposes the whole panel, i.e. individual layers of the panel may be dyed according to industry practices (e.g. green for panels with enhanced moisture resistance, or red for panels integrally treated with flame-retardant chemicals).
Integral colouring is distinct from the voluntary coloured stripe system that may be applied on the outside edge of panels in a pack, at opposite corners to identify particular grades in accordance with EN standards.
Density, Mass and Sheet Size
Standard forms of MDF have densities as follows:
Average density: 700 - 800kg/m3
Core density: 600 - 700kg/m3
Face density: 1000 - 1100kg/m3
These are now considered to be part of a wide range of dry-process fibreboards with the following densities.
HDF: Above 800kg/m3
LDF: Below 650kg/m3
ULDF: Below 550kg/m3
Due to variation between brands, the weight of MDF is not constantly proportional to thickness. Typical weights, based on standard MDF with average density 750kg/m3, are:
Thickness
|

|
Mass per Unit Area
|
6.5mm
|
|
5.0kg/m2
|
9.0mm
|
|
6.3kg/m2
|
12.0mm
|
|
8.4kg/m2
|
16.0mm
|
|
11.0kg/m2
|
19.0mm
|
|
14.0kg/m2
|
MDF is available in an extensive range of thicknesses, i.e. 1.8mm to 60mm. The most common sheet sizes are: widths 1220mm, 1525mm and 1850mm and in lengths up to 3660mm.
Other sizes are available or can be produced to order (minimum order conditions exist). With the exception of the largest users such as volume furniture manufacturers, MDF in common with other wood-based panels would generally not be supplied direct by the manufacturer but instead depending on the volume and specification could be supplied through a distributor or merchant.